Continuous upgrading and innovation of aluminum melting and casting technology
Aluminum melting and casting technology mainly refers to the various technologies involved in the production process of sheet, strip, foil and tube, rod and profile blanks. Technologies such as soaking, sawing, testing and automation and intelligent integration. At present, the most basic equipment configuration of a casting workshop includes melting and holding furnace (or aluminum melting furnace and holding furnace), launder, online processing system, casting machine, etc.
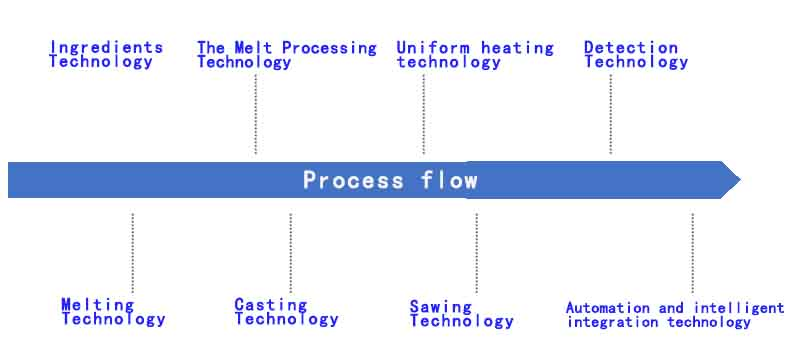
From the actual production status of the casting workshop, the main operations include feeding, slag removal, feeding, refining, mold repair, cleaning, lifting, transporting, placing, loading and unloading, baling, loading, etc. In addition, there are also There are liquid feed, solid feed, furnace side refining and so on. In actual operation, the current aluminum leakage detection and plugging in the casting stage still require manual labor, which requires a large workload and a high risk factor. In addition, manual operations are also required for purging and mold maintenance after the end. In comparison, most of the work such as automatic control and hanging ingots has been solved. After casting and hoisting out the ingots, through the storage roller table, sawing machine, soaking furnace (including soaking chamber, cooling chamber, feeding car, etc.), automatic stacking and stacking system (stacker, stacker, transfer day) Vehicles, etc.), flaw detectors, weighing, baling, loading and other systems are supplemented by the MES system to connect the entire process to achieve intelligent and continuous production.
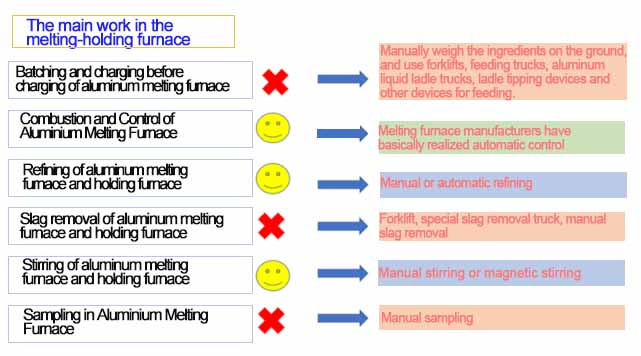
Therefore, at present, there are still problems such as uneven equipment configuration and poor logistics links between production lines. However, with the development of technology, the combined application and coordination of equipment are currently linked through different management systems, and the production efficiency is improved. It has been improved, and the casting workshop has developed towards intelligence.
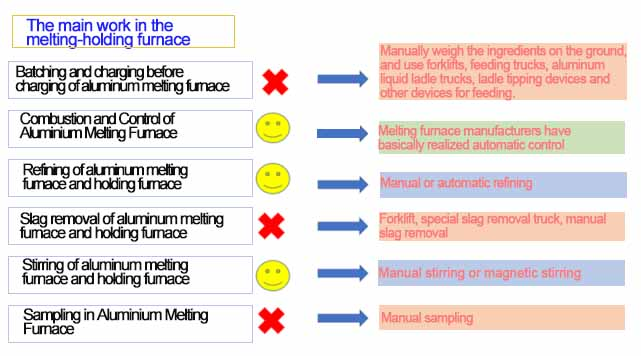
From the current situation of the application of aluminum melting and casting technology, the technologies currently used mainly include melting heating technology, melt processing technology, casting technology, and other workshop technologies. The most commonly used melting heating technology is regenerative combustion and high-speed burner combustion in gas heating, in addition to electric heating and circulating heating. Melt treatment technology includes pre-furnace treatment, in-furnace treatment, online degassing, slag removal, grain refinement and other technologies. Casting technology includes flat ingot, round ingot, casting and rolling strip technology, and other workshop technologies include soaking technology, cooling technology, sawing technology and so on.
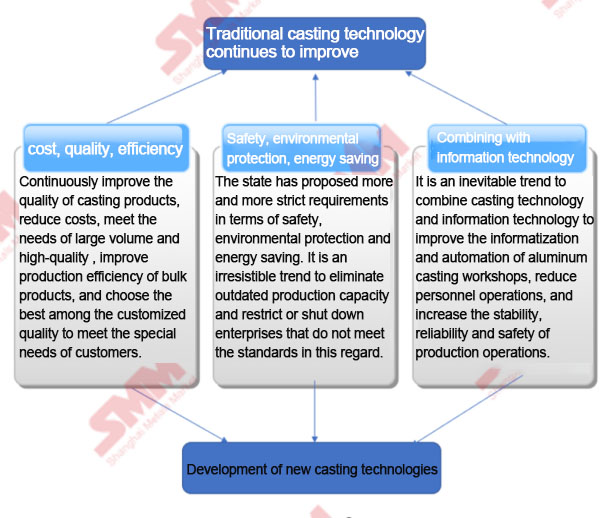
At present, the current development of casting technology is mainly due to the coexistence of multiple casting technologies, and the requirements for products in terms of cost, quality and efficiency are as high as ever, while the requirements for environmental protection, energy saving and safety are gradually strengthened. As new technologies continue to emerge, outdated technologies are gradually phased out.
With the needs of competition in the industry, the regulation and guidance of national policies, and the continuous improvement of casting technology, it not only pays more attention to reducing costs, improving product quality, and improving production efficiency, but also pays more attention to environmental protection, energy saving and safety requirements. The combination with information technology has become an inevitable trend.
Cost reduction, efficiency enhancement, environmental protection and energy saving are the main development directions of new aluminum casting technology
Among the feeding and slag removal technologies, there are mainly automatic feeding vehicles and automatic slag removal vehicles. It is used for the operation of adding solid material, liquid material and slag skimming before the furnace.
The alkali removal device in the melt processing technology is used for the pretreatment of the electrolyte in front of the furnace, and the refining vehicle refining technology is used in the front of the furnace instead of manual refining to improve safety. The furnace side rotary degassing device is mainly used for refining in the furnace, which does not require human intervention, effectively improves efficiency, and also improves safety. In addition, the electromagnetic filtration
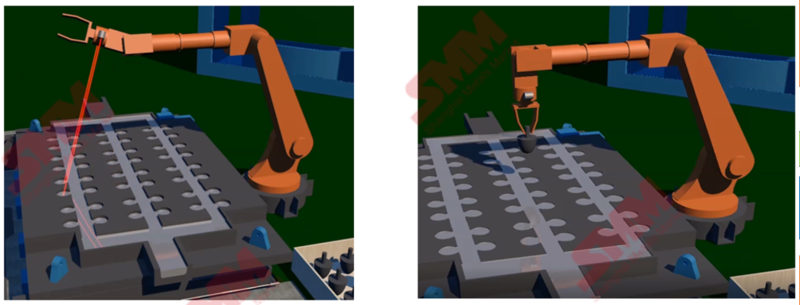
device is mainly used for online filtration, which has the advantages of higher filtration accuracy, basically no impurities introduced, and easy disassembly and installation. The ultrasonic degassing device can realize the introduction of no impurities, the removal rate of hydrogen is as high as 70%, and the grains can be refined while refining.
Under the basic requirements of continuously obtaining higher-quality aluminum alloy melts and billets, melting and casting technology needs to further meet the requirements of bulk product production efficiency and customized product quality. The popularization of workshop automation and intelligent production can greatly improve production efficiency and meet the needs of bulk products. At the same time, accelerating the promotion of the latest melt purification technology and casting technology can effectively improve the quality requirements of customized products, and finally supplemented by intelligence and automation. Integrated technology fully improves the stability, safety and reliability of workshop production, and ensures the advanced nature of the workshop in terms of environmental protection and energy saving
Post time: Aug-15-2022